CC joins with others to create needed visors and shields
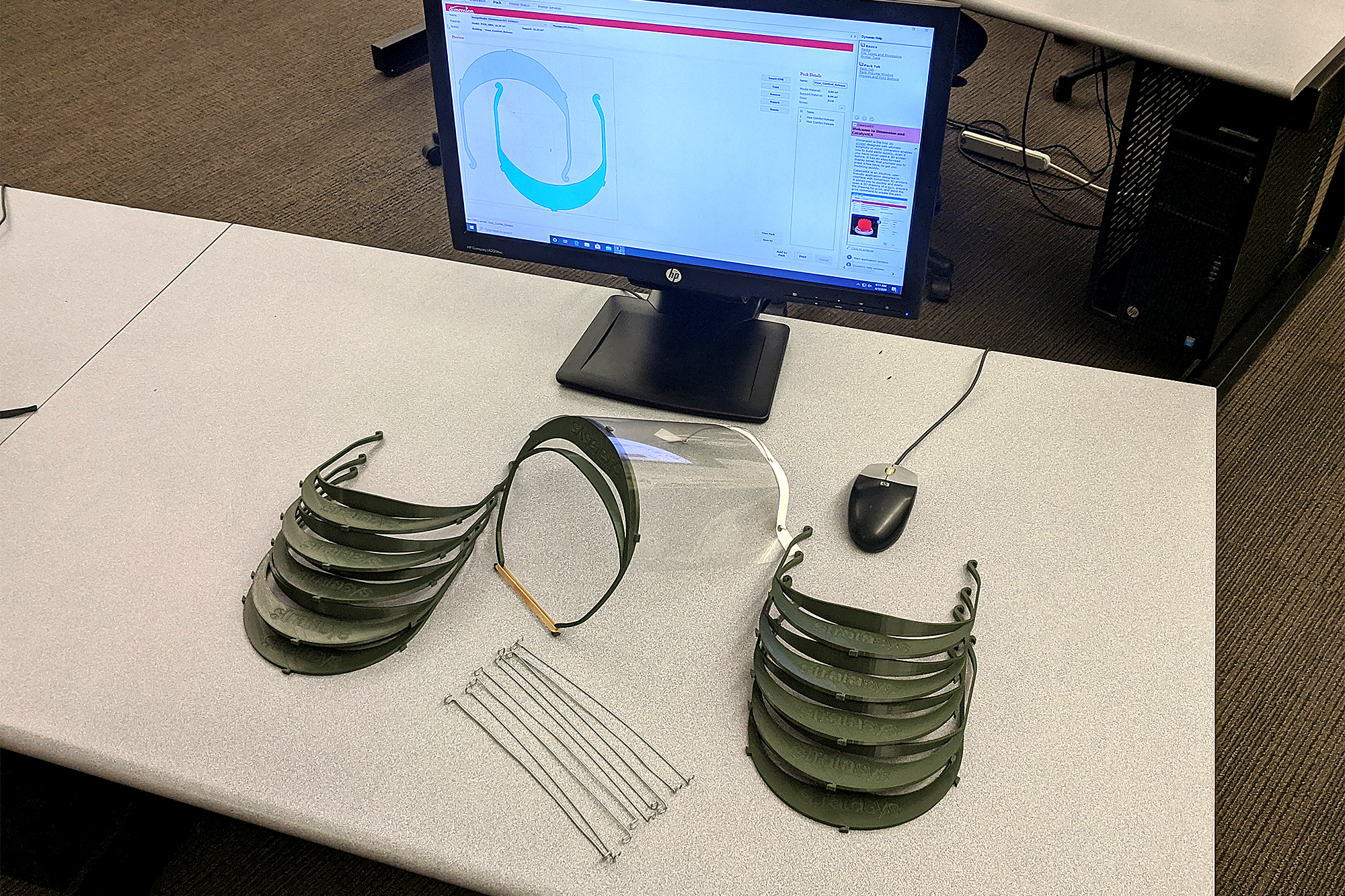
One day in late March, Paul Brutsman found himself part of an email chain. The thrust of the email in that chain was that the Wyoming Medical Center needed medical-grade face shields.
Brutsman, an engineering technology and design instructor at Casper College, felt that the college, with help from others, could probably produce the shields. After visiting with Mike Staley, senior vice president and chief administrative officer at WMC, Brutsman began work on the project. That work involved not only Casper College, but Woodworker’s Supply employees Jay Sanger and Gary Hiatt; two career and technical education instructors, Kora Huffman from Kelly Walsh High School and Jim Fulkerson from Midwest School; and Casper College students David Terrell, Richard Orndorff, and Lucas Mauro.
“Once I knew exactly what they were looking for at WMC, I started visiting with a variety of people,” said Brutsman. The entire head covering consisted of two parts: the visor portion that an individual shield would insert into, and the shield itself. Brutsman was able to come up with a material that would work for the shield part, overhead projector transparencies. He found a whole box of new ones, in fact, in his file cabinet.
“The visors will be used repeatedly, while the shields will typically be used once,” Brutsman said. The visors are created out of a durable plastic material and fit easily on the top of a forehead. The piece comes with three projections that the shield, which is three-hole-punched, fits securely over. The first difficulty to overcome would be the flexibility of each transparency sheet. Sanger and Hiatt suggested to Brutsman that a thin, flexible, and inexpensive piece of wire be used on the bottom of the transparency to provide stability.
The next problem was how to use the wire with the transparency. Brutsman discussed the issue with his “Mechanical Design II” students, Terrell and Orndorff, who came up with a way to easily loop a flexible piece of wire to the bottom of each transparency. Brutsman said, “By doing this, we were able to create a curved shield with stability that wouldn’t twist and turn if a bit of wind hit it.”
A prototype was created, and according to Brutsman, Staley was pleased with the results and asked him if 50 visors could be produced for the hospital. This request led to Brutsman’s next partnership with KWHS and Midwest.
The college has one 3D printer, but it takes approximately 90 minutes to print one visor, said Brutsman. He reached out to Huffman and Fulkerson to see if they would be able to help by printing visors on the 3D printer that each school had. They both were eager to help and were permitted to bring the printers home to print visors throughout the day as both are teaching online from their homes. Missing from the group was Kyle Dye, who teaches career and technical education at Natrona County High School and Pathways Innovation Center. “I really wanted all of the high schools in Natrona County to participate, but we just couldn’t get the design to fit those printers. We tried scaling down the design, but then it made the visors too small to fit properly,” noted Brutsman.
Because of the size of Casper College’s 3D printer, Brutsman was not able to take it home. Instead, he had Mauro, who is also a work-study for the department and has been laser-cutting fabric for face masks, keep track of the printing process.
On Monday, April 13, Brutsman was able to deliver 60 visors — 20 each from Casper College, KWHS, and Midwest — and 100 shields to the WMC. “It’s not often that you get a chance to work with so many different individuals on one project, but it was a very neat thing to do with them,” said Brutsman.